Leave the job to the experts!
Neuros Co. was founded in the early 2000’s and within a bright more than a couple of decades long history and work experience at manufacturing High-Teck Turbo Blowers/Compressors which were installed in more than 5000 operational units around the globe in 18 different countries worldwide which should be noted that more than 670 of those units are located in North America U. S.
Neuros Co. has shown a bright history and a leading step on the Turbo Blower/Compressor design + manufacturing ground.
More About Company
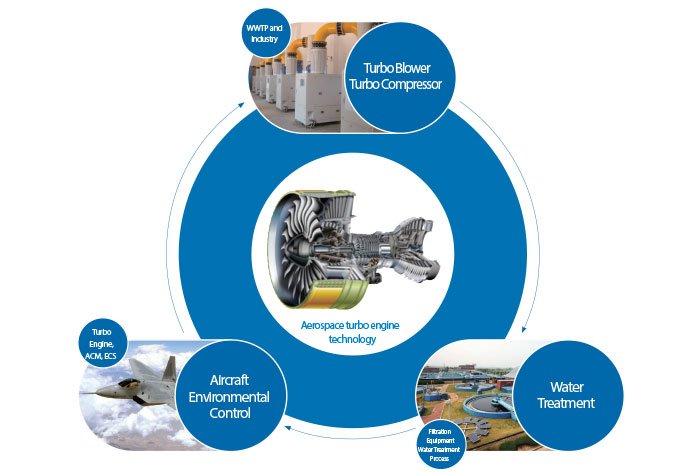
Figure (1): Neuros Modeling Cycle, Design & Performance of Turbo Blower/Compressor
Neuros Co. used the technology and design of fighter jet’s turbo engines as a model which means they used the two basic and advanced technologies of the turbojet engine industry:
- Environmental Control System (ECS)
- Air Cycle Machine (ACM)
The two which has been mentioned were previously only in the American military aerospace industry’s Monopoly but today thanks to Neuros innovation the cards have turned in the industry.
It is worth mentioning that the National Aero-Space of America (NASA) used both technologies through an advanced method of Air Bearing to prevent and control the bearing stresses between impeller and shaft.
Neuros uses the best kind of Fluid bearing which is Air bearing that makes durable and suitable lubrication for high rotation speeds and high temperatures which can be considered as a tremendous revolution in the design and manufacture industry of blowers and compressors
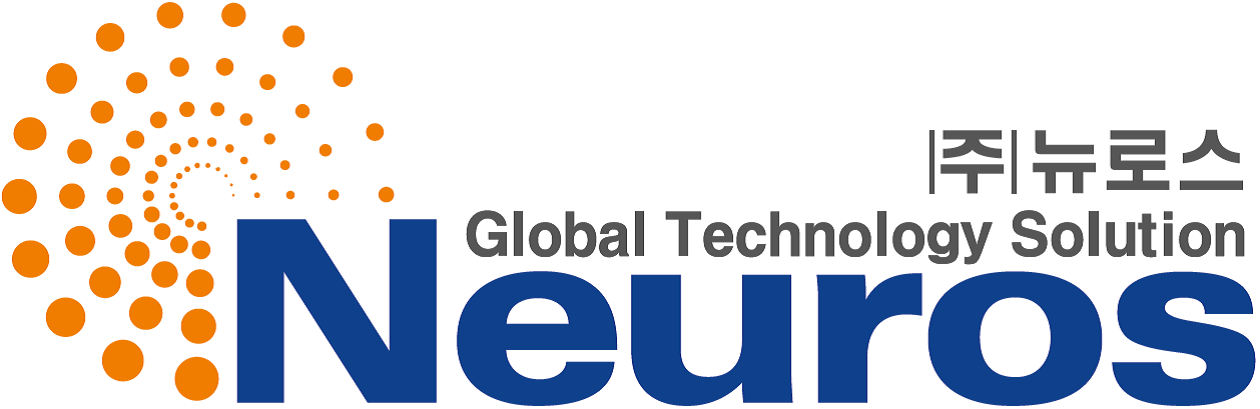
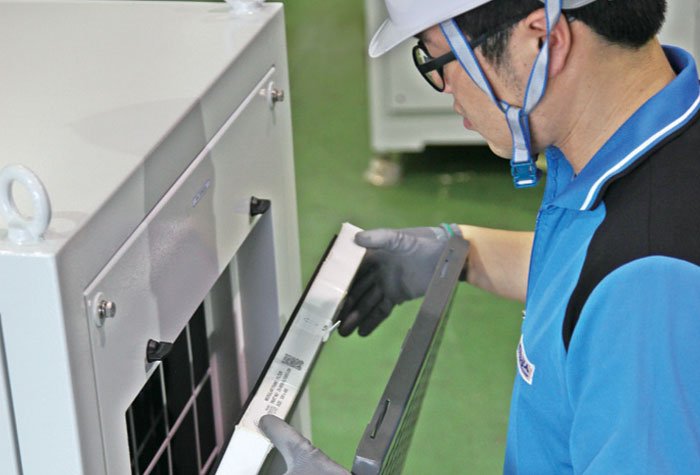
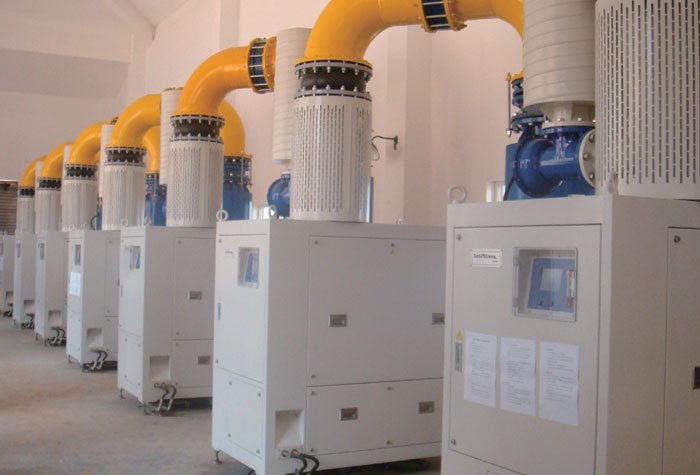
Turbo…Or not Turbo?
Basically, the first question that comes right to our customer's mind is, what is the massive difference between turbo blowers and their common counterparts which is positive displacement blowers (D.P)?
Well, there should be no worries because we have the answer of course not with spice or praise and exaggeration but actually with reliable reasons and statistics!
For that cause, first, we have to explain the parts, structure, and design of turbomachines to make a better concept and understanding of the scheme and the differences between the turbos and the common ones.
The design of aerodynamic centrifugal compressor (impeller) with high performance
Figure (2): Impeller and the spread of stress on its different coordinates
- The aerodynamic design of the impeller and diffuser plays a key role in function increase
- Impeller structure integrity has been confirmed to be tested at 120% rotational speed in a rotation test.
- The most suitable material has been used in high speed for manufacturing parts, Aluminum alloy is the main substance but if customers order, using Titanium and sustainable steel (SUS) or Japan industry of steel (JIS) is possible. It should be noted, the impeller is machined by five-axis CNC devices with 0.001mm tolerance to minimize blade tip cleaning.
- More integrity results in more life cycle plus longer diameter with an accurate shape of the impeller which will cause an optimal special speed that can increase the function
- To increase the durability and resistance against corrosion a thick coat of anodizing is put on the impeller
M.S.M (Self-developed Permanent Magnet Synchronous Motor)
Figure (4): Rotor (left side) & Stator (right side)
Neuros Self-Developed Permanent Magnet Synchronous Motor (PMSM) is the most suitable solution for high-speed operations which has been proved to have high efficiency and a power factor of more than 95% with low current drop; Thanks to the direct connection between rotor and impeller (coaxial), the complex weight has been decreased and we have a negligible mechanical loss during operations which is strength point in function increase.
Figure (5) Engine Structure
Engine Technical Specifications
- Power:30-300 HP
- Rotor Speed: 10000-100000 RPM
- Efficiency:95%
- Electronic Factor:90-95
- Polars:2
- Insulation Class: H Class
- Cooling: Air
- Operation: Continues
- Protection Index: IP55
* IP55 engine general protection standard: figure 5 tens: protection against dust intrusion protection against dust and soil penetration into vulnerable parts, figure 5 unit: protection against radial splashing of water in all directions, water eruption
* Thermal class (insulation) of H CL engine: 180'c glass fibers, asbestos with silicone gums, pure silicone varnishes
VFD (Variable Frequency Drive)
With variable frequency drive (VFD), through the control of the rotational speed of the magnetic synchronous motor (PMSM), in order to adjust the pressure and the amount of discharge current, for the customer's needs that in a wide operating range of 45-100% can be energy loss from Destroyed.
Air Bearing
An air bearing is a non-contact compatible bearing that is formed when the air film is automatically generated by the hydrodynamic interaction between the cohesive fluid and the foil structure in a rotating sleeve or disc. These bearings are classified into two types of bump (BUMP) and leaf type (LEAF) based on the foil configuration.
Figure (6) Production of hydrodynamic pressure
As the rotor accelerates, a thin layer of air forms a cushion between the shaft and the bearing surface.
Figure (7) to the right of the leaf model (Leaf) and to the left of the bump model (Bump)
As we mentioned in the introduction, Neuros company, inspired by ACM & ECS technology, has created an amazing innovation in the design of new generation blowers and compressors, namely the use of thrust bearings, which are in the form of thrust bearing and journal. Bearing) is used.
Figure (8) Air Journal Bearings Figure (9) Air thrust bearing
Figure (10) Overview of rotor and impeller connections
Table (1) Comparison of air bearings with conventional bearings
Neuros
Dahi Bondad has been recognized with supplier and manufacturer awards from some of the world’s top companies and clients. Join the pool of satisfied clients now!

Turbo Blower

Turbo Compressor
Project portfolio
We have decades of experience meeting the stringent regulations and certifications for the automotive, aerospace and medical device industries, which serve as benchmarks for all of the products we manufacture.
Projects
- All
- Rotary
- Steel and Mineral
- Water & Wastewater